The boat is with the same fine lines as her little sister. However the aft ship is changes a bit to make the boat more suitable for a large outboard, a possibility that has been much requested for the 15' Dinghy. So the 18' Dinghy will carry an outboard up to 20 hp (recommended minimum 5 hp), so there should be plenty of speed potential.
The extra 3 feet has been used to make a real outboard well aft and making the seats wider and more comfortable. Due to the innovative use of the plywood it succeeded to make this version without the intermediate frames, making the passing from one thwart to the next without any obstacles.
Main dimensions:
Length overall = 5,480 m
Beam = 1,456 m
Depth = 0,859 m
Draft = 0,150 m
Displacement = 612 kg / 1349 lbs.
Hull weight = 85 kg / 187 lbs.
Passengers = up to 4
Outboard = 5 - 20 HP
I live in Davao City in the Philippines and I think this boat will work very well on my Samal Island beach property. It will be used for fishing, sightseeing and transportation.
I bought the plywood on November 18, 2008 and now it is lofted and awaiting assembly. From five sheets of 5mm I have 59.5 lbs. of pieces. The 9mm stock yielded 100lbs of cut pieces for a total of 160lbs of cut plywood. Morton stated the weight of the finished boat is 187 lbs. Even though I used 5mm plywood instead of 6mm I doubt I can match that. I will be glassing all of the seams of course as well as the exterior. Then paint will add weight. I bought some plastic film as used for covering books to place over the fiberglass butt seams for the hull panels. After finishing the fibreglass and before it sets I place the plastic film over the work and add a flat sheet of galvanized iron with added weight on top. I believe this will make much smoother seams. I will be using a strongback to hold the frames in their exact spacing.
I have ordered oarlocks from Duckworks in the USA and they are on the way. I am also looking to have someone bring back a small Danforth anchor. With chain that seems to be enough to hold this dinghy. I have also started the process of ordering an eight horse Yamaha from Manila.
Today since I had finished butt joining the bottom panel I started making the strongback. Using my workbench as a strongback made the whole process easy. Although about a foot short I was able to extend the workbench to make a connection to the last seat frame. Then I placed the bottom panel on top and re-measured all the spacing and after adjustments temporarily secured the panel with nails. I am continuing to butt join all the panels and that takes time. I have been doing about 1 panel per day. I now have two more panels to join. The size of this project is pushing the limits of my shop.
This is my shop area and workbench. The workbench will be the strongback.
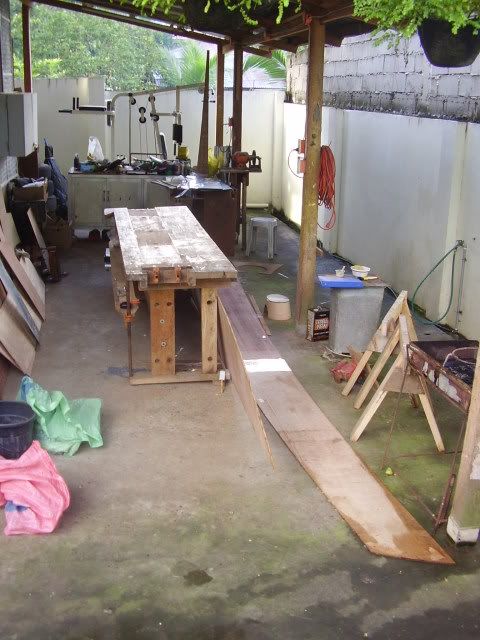
This is the butt spliced 9mm bottom panel.
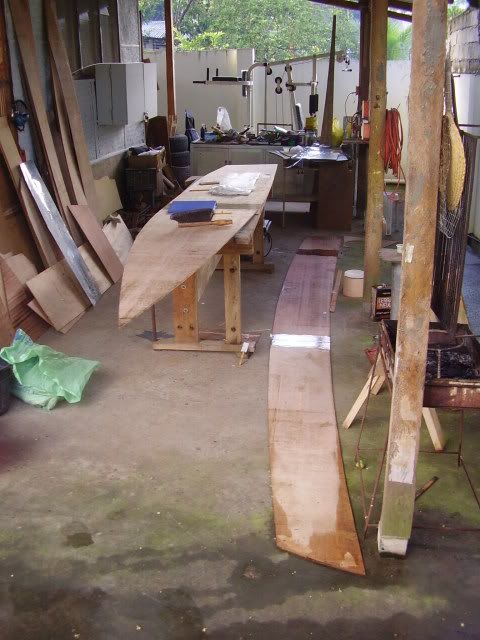
Only four of the seven frames can fit on the strongback, this is a long boat.
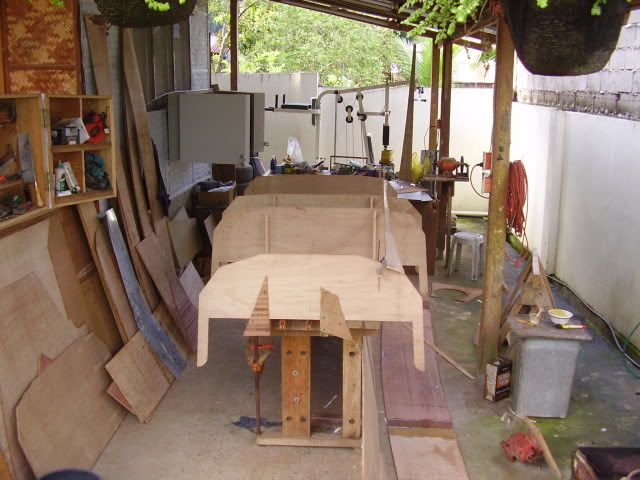
Here the bottom panel is adjusted on the frames. This surface is now my temporary workbench.
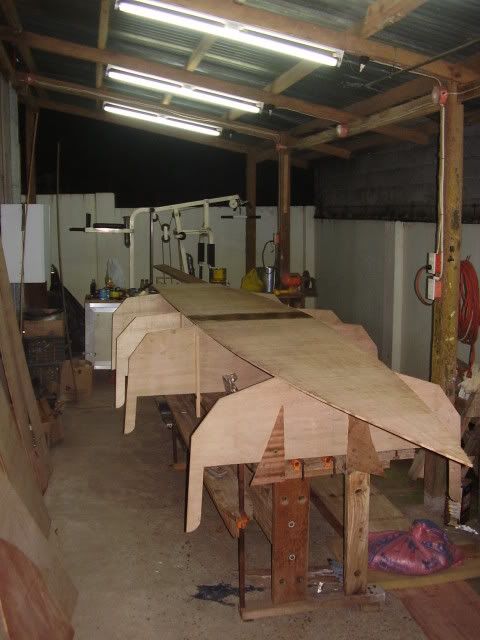
This is the back view showing my workbench extension for the frame E.
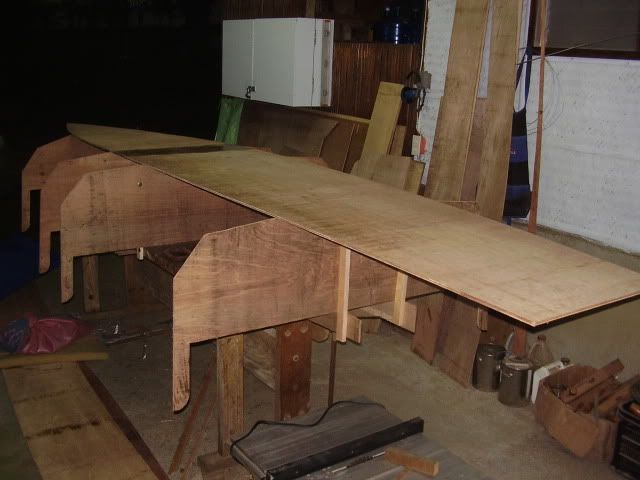